Introduction
Ipex Green Safety non-pressurised powder fire-suppression dispenser discharger
Active fire protection measures are based on the use of a range of substances capable of interrupting combustion.
The substance used, the type of intervention and the way it is used must be commensurate with the nature of the products that have caught fire and the extent of the fire.
It is important to know whether or not the extinguishing agent can be used on live equipment.
Therefore, it is necessary to be familiar with the characteristics of the extinguishing substances in order to always obtain positive results from active protection, bearing in mind that the wrong choices can lead to magnifying the extent of the accident.
Some of the substances used today are as old as humanity; others have been discovered more recently and are the result of ongoing research into increasingly effective methods and systems for fighting fires.
Such research is all the more necessary as modern techniques and processes lead to ever greater quantities of dangerous or easily combustible products being concentrated in restricted areas.
Extinguishing powders are mixtures of finely divided solid particles consisting of organic salts or other natural or synthetic substances suitable for being discharged directly onto fires. There are numerous powders available, some of which are universal and others specific.
The powder used by Green Safety dispensers is a mixture of monoammonium phosphate, sodium and potassium bicarbonate and anti-caking agents to improve storage, fluidity, water repellence and in some cases compatibility with foams. Green Safety's rapid discharge dispenser powder is suitable for extinguishing fires involving solid combustible materials, flammable liquids, gases and electrical equipment – classes A, B, C & E.
Extinguishing action
The mechanism that determines the extinguishing of a fire, by powders, is a combination of different effects that, when carried out simultaneously, determine the inhibition of the combustion process:
- Smothering: ddue to the covering or layering action of the dust.
By depositing itself on the ignited and unburnt parts, it practically isolates the ignited material from the combustion agent and renders the non-combusted material inaccessible.
In addition, in certain powders, the chemical reaction between the substances of which they are composed and the fire develops carbon dioxide, which has a smothering effect, replacing the oxygen in the air. - Cooling: due to the lowering of the temperature of the fuel below the ignition temperature, either as a result of cooling due to heat absorption by the extinguishing agent or as a result of the aforementioned chemical reaction.
- Negative catalysis: due to the high temperatures reached in the fire, decomposition occurs with a consequent anti-catalytic action. The substances contained in the powders interact with the H+ and OH- free radicals to form stable molecular structures, resulting in the reaction chain being broken and the fire being definitively extinguished.
This justifies the great effectiveness and high speed of action of powders, particularly when compared to the limited quantity of substance required to achieve extinction. Chemical powders are one of the most versatile extinguishing agents; they can be used on fires involving various types of fuel such as wood, paper and even alkali metals such as magnesium.
In any case, for each type of fuel, it is necessary to apply the type of powder capable of best performing the extinguishing function.
In particular, the "polyvalent" powders (based on monoammonium phosphates) are suitable for class A, B and C fires.
Monoammonium phosphate powders decompose under the action of heat, leaving a residue which prevents contact with oxygen and thereby prevents reignition.
Mechanism action
After a thorough study of the state of development of currently used fire-suppression systems and an analysis of their advantages and disadvantages, Green Safety, using the latest findings from the international fire-suppression industry, identified the IPEX series of dry powder dispensers as a state-of-the-art, multi-purpose and cost-effective fire-extinguishing product.
The high performances of the IPEX modules have been obtained thanks to the use of:
- Devices that generate low-temperature gas called cold gas sources (CGS).
- A fine-grained powder extinguisher (guaranteed for 10 years for installation in environments with an ambient temperature range of -50 °C to +90 °С) that extinguishes fire via a dual action method – surface and volumetric).
Green Safety's dry powder dispensers are non-pressurised and generate an extremely fast discharge of the extinguishing agent (less than 5 seconds) to the fire zone, making them suitable for extinguishing fires in both enclosed and open spaces.
They produce atomisation of the powder during discharge and ensure a double action of both volumetric and surface suppression and consequently instant fire suppression. Non-pressurised dispensers provide the added advantage of simple installation, low maintenance and the ability to be installed within the area to be protected. This type of dispenser consists of a container which is filled with a dry powder capable of extinguishing class A, B and C fires. Inside the container is a gas generator with an electrical activator. A special membrane is connected with a discharge nozzle to a special flange.
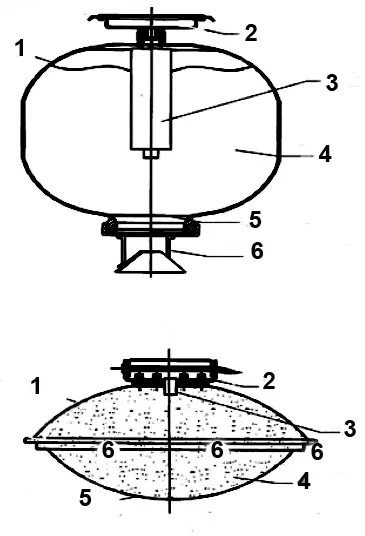
- Metal container
- Flange
- Gas generator with an electrical activator
- Solid extinguishing agent
- Membrane
- Discharge nozzle
Intended use
The dry powder extinguishing agent is suitable for extinguishing fires in enclosed environments, the risk of which is constituted by the presence of:
- Solid combustible materials (Fire class A) such as wood, paper, textiles, composite materials, plastics and others.
- Liquid combustible materials (Fire Class B) such as lubricating oils, petrol and other petroleum refining products, organic solvents, resins, etc.
- Fires involving flammable gases (Fire class C) such as methane, propane, LPG, chlorine, coal gas, acetylene, hydrogen, methyl chloride, etc.
- Electrical and electronic equipment, including those under voltage, up to 20KV such as: electrical panels, dry-type and oil-immersed transformers, cable tunnels and cable galleries, transformer and distribution cabins, electronic telephony equipment.
Limitations of use
Dry powder extinguishers are contraindicated when substances that react dangerously with powder such as alkaline cyanides are involved; they are not recommended in open spaces or when very delicate equipment is involved, as the powder may damage it.
The use of powders on sensitive electrical or electronic equipment is not recommended as the extinguishing agent will seriously damage the equipment; it is better to use "clean extinguishing agents".
The use of powders requires a thorough cleaning of the parts affected by the "cloud" after the intervention and is therefore not recommended for particularly complex and delicate equipment.
Care should be taken when inhaling because although it is not toxic, it can still cause irritation of the respiratory tract.
The designer, in the design/specification phase, must provide for any mechanical ventilation system if they consider that the existing ventilation is insufficient and/or unsuitable for post-discharge clean-up of the room.
Actions to be carried out after the discharge
In the event of an untimely discharge, it is important to ventilate the premises promptly, if possible not later than one hour after discharge, in order to avoid excessive powder deposit on flat surfaces. If there are no openings to the outside, an extraction system must be provided. The better the post-discharge ventilation, the lower the amount of product deposited. The removal of the deposited residue must also be carried out promptly. In the event of accidental activation in the data processing centre, it is advisable to cut off the power supply to the equipment.
There are several actions to be taken, depending on the materials and surfaces involved.
- a) Material involved: paper or other hydrophilic surfaces.
For cleaning, use a cotton swab slightly soaked in distilled water. It may be necessary to repeat the treatment several times to ensure complete removal. Note: Paper exposed to dry powder discharge may turn yellow.
- b) Material involved: particularly delicate electronic equipment.
Ensure that the electrical circuits are cleaned as soon as possible. It is the responsibility of the end user to determine the techniques and methods for removing the extinguishing product and whether to use their own trained personnel or a specialised external company. It is recommended that all equipment subjected to discharging should be switched off and only switched on again once it has been successfully cleaned.
- c) Surface: metal plate
For cleaning, use a wet paper towel with degreasing detergent (with added bleach)
- d) Surface: floors
For the cleaning of a normal floor – where possible – the use of a vacuum cleaner and washing with normal cleaning agents (broom, mops, detergent etc.) is sufficient. - e) Surface: other flat surfaces.
Where possible, use a vacuum cleaner and the usual dusting cloth.
The above only applies to discharges in the absence of a fire that occurred due to incorrect operation of the system.
Once the room has been ventilated, the staff must wear the following PPE for cleaning operations (minimum level): long-sleeved latex gloves, filtering face masks and box-shaped eye masks. To enter the room immediately after the discharge, staff must wear the following PPE (minimum level): polypropylene TNT overalls with elasticated face, wrists, ankles and waist with hood, long-sleeved latex gloves and full face mask with anti-dust (UNI EN 143) and anti-gas (UNI EN 141) filters.
Note: Maintenance, combined with constant and thorough cleaning of the equipment and related components (cooling fans – boards, etc., to prevent accumulation of dust and/or sediment) help to prevent post-discharge inconvenience. In some cases dust, sediment, particulate matter from the extinguishing agent and ambient humidity could cause blockage of cooling fans.